Allzweckwaffe gegen Maschinenstillstände
Archivmeldung vom 12.06.2019
Bitte beachten Sie, dass die Meldung den Stand der Dinge zum Zeitpunkt ihrer Veröffentlichung am 12.06.2019 wiedergibt. Eventuelle in der Zwischenzeit veränderte Sachverhalte bleiben daher unberücksichtigt.
Freigeschaltet durch Manuel Schmidt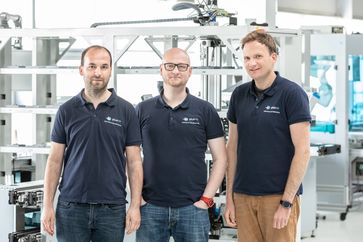
Forscher des Fraunhofer IPA haben ein Analysetool entwickelt, das dank selbstlernender Algorithmen Defekte in schnelltaktenden Fertigungsanlagen findet, bei der Fehlerbehebung unterstützt und ein automatisiertes Maschinen-Benchmarking durchführt. Nun machen sich die Wissenschaftler mit dieser Technologie selbstständig.
Vor allem die Pharma- und Konsumgüterindustrie arbeitet mit kapitalintensiven Fertigungsanlagen und ist darauf angewiesen, die Produktivität stets zu maximieren. Andernfalls drohen Kostendruck und Finanzierungslücken. Allerdings gilt in der Praxis: »Je komplexer die Anlage, desto geringer die Produktivität.« So bringt es Felix Müller, Gruppenleiter Autonome Produktionsoptimierung am Fraunhofer IPA, auf den Punkt. Hinzu kommt, dass viele Fertigungsanlagen eine Vielzahl an Stationen umfassen und so schnell arbeiten, dass Fehlerursachen mit bloßem Auge nicht erkennbar sind.
Mit der »Smarten Systemoptimierung« haben Müller und sein Team deshalb ein
Analysetool entwickelt, das Fehler und deren Ursache in schnelltaktenden, verketteten Fertigungsanlagen kontinuierlich erkennt: Ein leistungsstarker Konnektor greift dazu über das jeweilige Herstellerprotokoll hochfrequent auf die Daten in der Maschinensteuerung zu. So entsteht eine kontinuierliche Datenbasis, die mehrere selbstlernende Algorithmen zeitsynchron auswerten. Diese erkennen detailliert, wo Fehler im Fertigungssystem vorliegen, wie sie zusammenhängen und welche Prioritäten sie bei der Behebung haben. Auf diese Weise können Defekte, die zum Ausfall des gesamten Systems führen, schneller behoben oder gar vorhergesagt werden.
System lernt kontinuierlich dazu
Allerdings ist nicht immer klar, was zu tun ist, wenn ein Fehler aufzutreten droht. Dazu kommen Folgemeldungen der Anlage, die die Situation für den Bediener noch unübersichtlicher gestalten. Aus diesem Grund haben Müller und sein Team Shannon® entwickelt, ein intelligentes Werker-Assistenzsystem für komplexe Fertigungsanlagen, das auf der »Smarten Systemoptimierung« aufbaut. Bisher oblag es oft den Maschinenbedienern zu entscheiden, was sie tun, um einen Fehler zu beheben. Nun aber schickt ihnen die betroffene Maschine eine detaillierte Schritt-für-Schritt-Anleitung auf das Smartphone oder Tablet. Die Datenbasis und die Verknüpfungen zwischen Störungen und Lösungen erweitern sich während des Anlagenbetriebs ständig.
So haben Anlagenbediener die Möglichkeit, selbst Anleitungen, etwa zur Behebung von Störungen, anzulegen. Diese Anleitungen können neben Text auch Fotos und Videos beinhalten. Weiterhin kann der Anlagenbediener Feedback zu den bereit-gestellten Informationen geben, was zur deren Verbesserung genutzt wird. Die Anlagenbediener sind auch aktiv aufgefordert Wissen einzubringen, beispielsweise bei der Beschreibung von detektierten, aber unbekannten Ereignissen. So baut sich mit der Zeit eine klar verständliche und durchgängig verknüpfte Wissensdatenbank auf, bestehend aus Fehlern, Ereignissen und Lösungen. Shannon® ist aktuell als Tablet- und Smartphone-App in mehreren Fabriken im Einsatz und hat dort die Zeit für die Behebung von Störungen deutlich verkürzt.
Effizienzsteigerung von bis zu 18 Prozent
Auch ein automatisiertes Maschinen-Benchmarking ist mit der »Smarten Systemoptimierung« machbar: In vielen Produktionshallen stehen dutzende identische oder ähnliche Maschinen und führen immer den gleichen Bearbeitungszyklus aus. Ein Beispiel dafür sind Spritzgieß-, Druckguss- oder auch Blasform- und Tiefziehmaschinen. Obwohl sie alle gleich aufgebaut sind, arbeiten manche langsamer als andere. Das liegt meist am Verschleiß bestimmter Bauteile, an variierendem Sensorverhalten oder unterschiedlichen Werkzeugeinstellungen sowie Materialschwankungen.
Beim Maschinen-Benchmarking wird zunächst der Gesamtablauf in einer Maschine definiert und in Einzelschritte aufgeteilt. Anschließend erzeugt der hochfrequente Konnektor an der Maschinensteuerung eine Datenbasis, die ein Machine-Learning-Algorithmenpaket auswertet. Dies geschieht mit allen angeschlossenen Maschinen gleichzeitig und wird rein virtuell zu einem idealen Prozessablauf verschmolzen. Daraus erkennt das Tool sofort, wenn eine Maschine langsamer läuft als vorgesehen und verknüpft dies mit einer technischen Ursache. Anwender können so nicht nur Störungen beheben bevor sie auftreten, sondern auch eine optimierte Zykluszeit für die angeschlossenen Maschinen erhalten, indem sie die besten Einzelschritte zusammenfügen. Dies führte je nach Maschine in den bisherigen Prototypenanwendungen zu Zykluszeitreduktionen zwischen zwei und 18 Prozent. Auch die bisher schnellste Maschine kann also noch schneller werden. Die Anwendung ist mittlerweile in eine kontinuierlich lernende Software namens Darwin überführt worden.
Forscher gründen Start-up
Bei mehreren Automobilzulieferern und einem Spritzgießmaschinenhersteller ist Darwin, das intelligente Maschinen-Benchmarking, bereits zum Einsatz gekommen, auch werks-übergreifend. Shannon® findet bereits Anwendung bei großen Automobil- und Pharma-unternehmen. Grund genug für Felix Müller und seine beiden Mitgründer Thomas Hilzbrich und Pablo Mayer sich mit der »Smarten Systemoptimierung« selbstständig zu machen. Ihr Start-up, die plus10 GmbH, unterhält aktuell Büros in Stuttgart und Augsburg und nimmt heute den Betrieb auf.
Quelle: Fraunhofer-Institut für Produktionstechnik und Automatisierung IPA (idw)